Net Zero Steel
Net zero steel is possible,
but it means that by the end of this decade
all new & retrofit facilities globally must be clean
The production of steel generates significant greenhouse gas emissions and is the largest single industrial global emitter after cement. In our efforts to move to a net zero-carbon world, steel has historically been treated as “hard to abate” or part of the “last 20% of emissions.” The objective of the Net-zero Steel Project is to counter this assumption and show instead that a decarbonization pathway for steel by 2050 is possible globally using technologies that are currently commercial, near-commercial and at the advanced pilot stage.
Facility level pathways by country are laid out that not only consider processes within each production facility but also the potential for solar & excess hydropower electricity generation and the availability of CO2 storage locations that can facilitate the transition to near zero carbon. A downloadable one page summary, policy brief, technical report, and country data sorted by facility are available. Ultimately this project seeks to provide a starting point for stakeholders to work towards net-zero targets and develop strategies that can support this transition through coordinated global innovation and commercialization policies and nationally appropriate uptake policies.
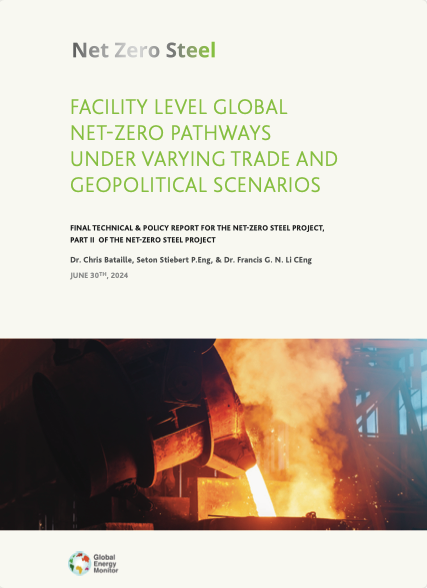
June 2024
TECHNICAL REPORT – PART II
FACILITY LEVEL GLOBAL NET-ZERO PATHWAYS UNDER VARYING TRADE AND GEOPOLITICAL SCENARIOS
Dr. Chris Bataille, Seton Stiebert P.Eng, and Dr. Francis Li CEngNew !
Key messages
- A global transition to net-zero CO2 emissions steel by midcentury is possible through maximizing volume and quality of recycled steel from 25 to 50%+ of production, paired with several possible near zero emissions iron ore reduction technologies
- Chinese capacity to make emission intense BF-BOF primary steel will soon exceed its demand. If Chinese firms can be persuaded to close the least efficient facilities with the worst air quality impacts this would leave more global market share for new clean iron ore reduction facilities, inside or outside of China.
- The next few years are critical to reorientate the global steel industry toward net zero emissions by mid-century. It takes at least 5 years from project inception to production for new iron ore reduction facilities, usually much longer, and any new reduction facilities built in the 2030s will be operating in the 2050s.
- Given most new demand for steel is outside developed countries, even a club of ambition that included the European Union, North America, South Korea, Japan, Australia and New Zealand (Narrow Club in this report), would not be large enough to transform the global steel industry by itself. This is true even if the rest of the world adopted significant carbon pricing policies (e.g., rising to $100/t CO2e by 2050). A broader club including for example India is required.
- Lead markets, especially for the first round of low GHG intensity iron ore reduction projects, are necessary to establish demand and investment certainty for clean iron ore reduction. This can be established through government preferred and subsidized procurement (e.g, through contracts for difference), through production tax credits like the IRA, or perhaps through something like the tradable Zero Emissions Vehicle mechanism, e.g., a Zero Emission Iron instrument.
- Reasonable cost finance is necessary to fund risky and expensive upfront investment, especially in developing countries. For at least the first round of projects in developing countries some form of risk reduction or concessional finance mechanism is necessary.
- Trade in low GHG intensity green hot briquetted iron (HBI) from multiple suppliers offers flexibility, security, and a means to transfer electricity and hydrogen consumption where it is cheapest and cleanest, as well as adding value to scrap for mixed primary & secondary production. We found it could reach at least 10% of global production, limited only by available iron ore resources. To reach its potential, however, it requires clear trade rules and tariffing that accurately assesses GHG intensity for all traded steel and iron.
GLOBAL FACILITY LEVEL NET-ZERO STEEL PATHWAYS - 2021
Technical Report – PART I
Dr. Chris Bataille, Seton Stiebert P.Eng, and Dr. Francis Li CEng
Methodology
We construct several transparent net-zero scenarios for the global steel sector based on projected demand, the retrofits cycle for steel plants, availability of scrap, access to CCS disposal geology, and solar PV and excess hydroelectric power driving hydrogen based steel making.
A detailed description of our methodology is provided in the technical report. The project method is summarized here.
Facility Database – We establish a database of existing 2019 facilities in 94 countries that includes age and current processes for making steel. We then dynamically and geographically add clean recycled and primary production when a minimum threshold of demand is met, eventually having steel production in 133 countries. By far the largest portion of steel making is in east Asia, with 54% of global production in China. We also derive facility-level production, energy use and emissions. Our boundary for direct emissions includes all direct energy and process emissions that typically occur at integrated iron and steel mills. We do not include upstream emissions (from the production of iron ore, processing of scrap steel off-site, and embodied emissions associated with the purchase of oxygen, lime, electricity and heat inputs) or downstream secondary manufacturing.
Decarbonization Options – We define deep decarbonization options for iron and steel production that will be incorporated into our pathways (Table 1 below). Given the needs for net-zero emissions economy wide by 2050, and based on the general practice of assessing CCS at -90% mitigation, we consider only options that are a maximum 10% of current emissions intensity. We do not consider the co-firing of BF-BOFs with hydrogen or the retrofit of BF-BOFs with CCS because these options only reach a 30-50% reduction in CO2 emissions.
Pathway Development – We project steel production demand to 2050 including material efficiency improvements, and then define how steel demand can be met through the retrofitting of current facilities and the building of new ones using deep decarbonization options using a transparent, algorithmic turnover of steel facilities to low emissions. This is based on estimates of each facility’s functional age since last build or last retrofit. Each facility is retrofit at the 25 year mark (we also test 32 and 40 years). We assume that carbon capture and storage (CCS) is preferable due to cost, and BFBOFs with CCS are preferable to syngas DRI EAFS because of familiarity of the industry with the BFBOF technology and its current ubiquity. Our allocation mechanism assumes:
- Carbon capture and storage (CCS) options are used when saline aquifer or depleted oil and gas wells are available nearby. Direct Reduced Iron with Carbon Capture and Storage (DRI-EAF-GAS-CCS), which is a currently commercial, is assumed until post combustion carbon capture and storage is mastered (BF-BOF-CCS ), assumed in 2030.
- If CCS is unavailable, we consider whether plentiful solar PV or excess hydropower are available at a reasonable cost to make electrolytic hydrogen for direct reduced iron (DRI-EAF-H2). Wind is not considered due to need for predictability for storage sizing.
If neither CCS nor solar PV/hydro generation are geospatially possible for existing production facilities, then “Non spatially allocated production” (NSP) is assumed. This could be new domestic or foreign new builds (as imports), or importation of green iron for use in EAFS.
In total we develop nine scenarios in order to consider three levels of long-term global steel demand and three lengths of available CO2 pipelines from existing sites. We also test the effect of longer retrofit cycles on the medium demand scenario. One assessment of scrap availability is used which allows for increased recycled steel use over time.
Steel production
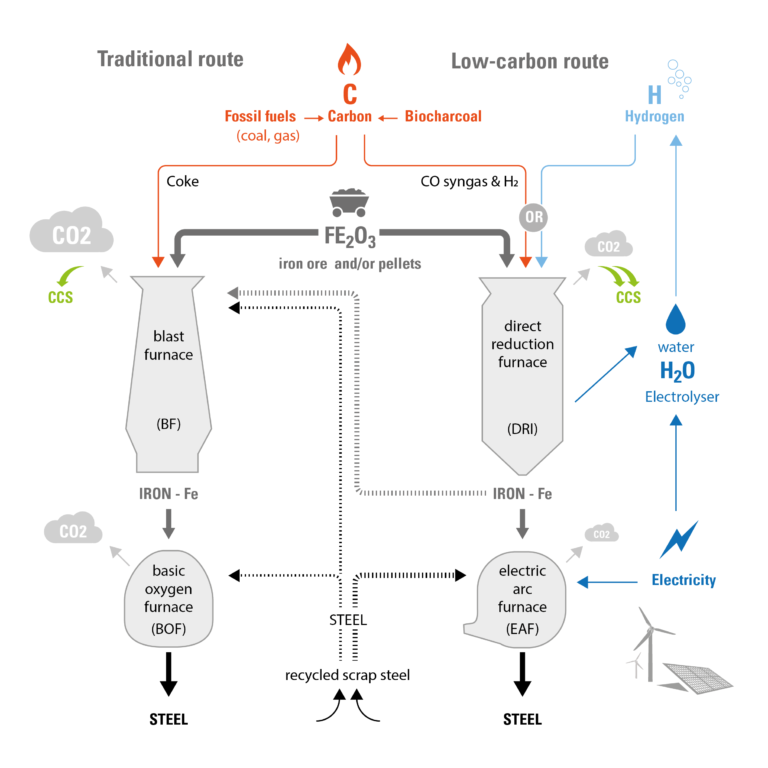
The technical means to net-zero steel
- More material efficiency in the making of vehicles, buildings, and infrastructure
- More recycling of steel products. Depends on supply of reasonable quality scrap and a network to gather it, using Electric Arc Furnaces (EAF) + Direct Reduced Iron (DRI) “sweetening” to reduce contamination (Technology Readiness Level 9)
- Blast furnace Basic oxygen furnace (BF-BOF) with 90%+ Carbon capture and storage, possibly with biomass TRL 5* (2030?)
- Advanced smelting with CCS (Progress has slowed, not shown, TRL 7 acc to IEA)
- Syngas based DRI EAF with concentrated flow CCS TRL 9*. Replaceable with 100% green hydrogen
- Green hydrogen DRI EAF TRL 7+ (2028-’30)
- Molten oxide or aqueous oxide electrolysis TRL 4 (2035-’40?) Not in diagram.
* Clean hydrogen blending would allow partial reductions, but it was not used in this project due to partial reductions.
Table 1: Processes included in technology scenarios
Green shaded rows represent decarbonization options (EAF assumes green sources of electricity)
Acronym | Name / Description | Use / Stage of Development |
BF-BOF | Blast Furnaces for reducing iron ore / Basic Oxygen Furnaces for smelting | Widely used, 70% of global steel production. |
DRI-EAF (GAS or COAL) | Direct Reduced Iron / Electric Arc Furnaces for smelting | 5% of global production |
OHF | Open-hearth Furnace | Limited use, mostly replaced by BF-BOF |
EAF | Electric Arc Furnaces | Widely used for smelting recycled scrap |
BF-BOF-CCS (90%) | Blast Furnaces for reducing iron ore / Basic Oxygen Furnaces for smelting with 90% Post-combustion Carbon Capture and Storage | Advanced development stage (TRL 5) |
DRI-EAF-GAS-CCS | Syngas direct reduced iron (DRI) with concentrated flow CO2 CCS followed by EAF | Fully commercial technology ready for market uptake (TRL 9). |
DRI-EAF-H2 | Green hydrogen (electrolysis with clean electricity) DRI followed by EAF | Prototype Stage (TRL 5-7+). |
Key Implications
This modelling exercise has several direct implications for climate policy with regards to steel makers.
Immediate Action is Critical
The lifetime of most emitting plants between substantial retrofits is normally at least 25 years. Therefore the 2020s and 2030s are critical. Many east Asian and specifically Chinese facilities are coming to their furnace relining date, when the core blast furnaces and basic oxygen furnaces must be shut down and rebuilt with new refractory linings, and this is the critical opportunity for substituting in low emitting iron reduction and smelting.
Limited CCS Potential for Existing Capacity
The need for pipelines to transport CO2 for storage put infrastructure limitations on the use of all types of Carbon Capture and Storage (CCS) globally. For many existing facilities, their supply chains and markets are simply not where the geological disposal is, and transport and more critical rights of way will be needed.
Siting of New Production
A substantial amount of demand globally cannot be met at existing sites with CCS or green hydrogen DRI (this is the wedge marked “NSP, or Non Spatial Production” in the Pathway results). This new iron and or steel production that must be sited in appropriate geographies for CCS or renewables based hydrogen production.
Green Opportunities
Countries with CCS geology and or renewable electricity generation potential have the opportunity to become a green iron & steel exporter, all the more so if they have plentiful iron ore compared to domestic needs (e.g., Australia, Brazil, Canada, South Africa, Russia).
Maximize recyclability
To maximum advantage of the growing recyclable iron product stock, vehicles, buildings, and infrastructure need to be designed to be taken apart at end of life in a way that allow high quality, low contamination recycling.
Material Efficiency
Our medium demand, low demand and recyclable scrap projections imply that there are building code, design & recyclability policies in place for material efficiency/circularity. The medium demand projection implies a 25% decline from today’s level of material intensity.
Decarbonization Commitment
Achieving a 1.5C compatible transformation requires a clear communication to steel makers that no more BFBOFs without 90% carbon capture can be built past 2025, and that manufacturers should be planning to invest in near zero emissions alternatives. This requires a multi-level policy commitment to transition to net-zero GHG industry. This in turn requires a transition pathway planning process including all key stakeholders to assess strategic & technolopgy options, competitive advantages, and uncertainties.
Innovation
Starting the process of clean replacement in the late 2020s requires a fast and effective global innovation process to commercialize green hydrogen DRI, which is partially underway in Europe and will likely meet the 2028 goal for several plants being operating, and BFBOF CCS, which is arguably going too slowly to meet the 2030 goal.
Commercialization Policy
Innovation implies accelerated R&D and commercialization – lead markets can be created with partners to build economies of scale with public and private green procurement, content regulations, supply chain branding, guaranteed pricing & output subsidies (e.g. contracts for difference). A systemic innovation and market uptake approach is needed, that includes new market design that values electricity system energy, capacity and demand response co-benefits in the business model.
Co-Benefits
Improved local air quality and reduced waste use benefits should be assessed as part of the transition. pathway planning process including all key stakeholders to assess strategic & tech options, competitive advantages, and uncertainties.
Infrastructure and Renewable Energy Investment
Spatial planning and investment is required to get the necessary rights-of-ways and infrastructure in place for the necessary CO2 pipelines. Investment is also needed to support additional solar or other clean electricity generation and facilities for overnight hydrogen storage.
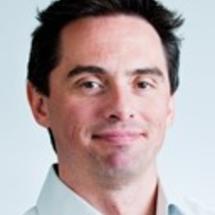
Dr. Chris Bataille
Associate Researcher, IDDRI.org, Paris / Adjunct Professor, Simon Fraser University, Vancouver, Canada
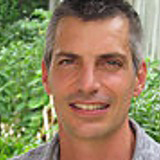
Seton Stiebert
Professional Engineer, Associate International Institute of Sustainable Development (IISD), Ottawa, Canada
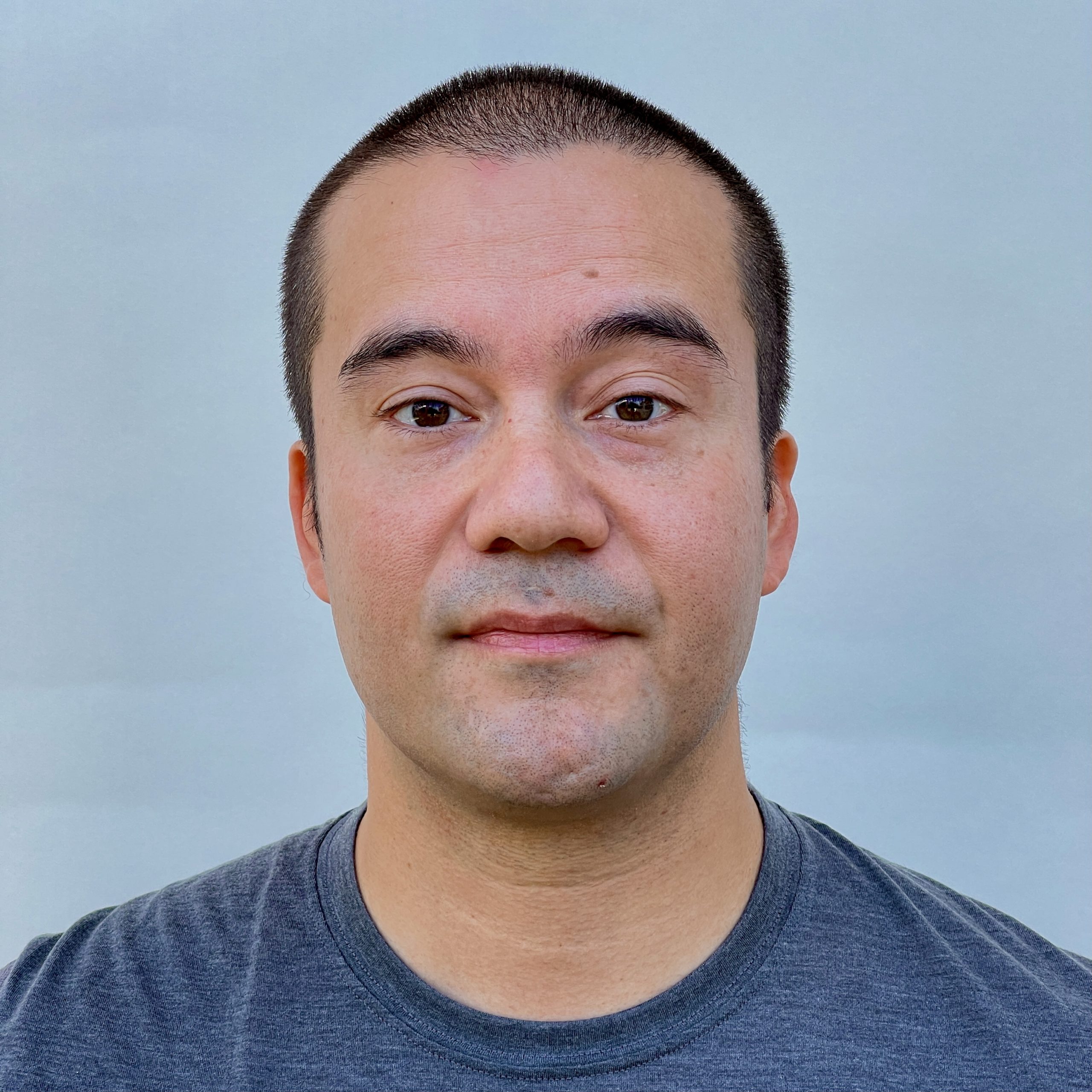
Dr. Francis Li
Principal Engineer, YarCom Inc.
Please contact Dr. Chris Bataille at info@netzeroindustry.org with any question.