Net Zero Cement
Cement industry is responsible for 1/3 of GHG emissions. Given the average economic lifetime of industrial facilities is 20 years or more, this indicates all new investment must be net zero emitting by 2035–2060 or be compensated by negative emissions to guarantee GHG-neutrality.
The cement industry is the second largest industrial CO2 emitter in the world, being responsible for around 7-8% of global CO2 emissions. Greenhouse gasses (GHGs) are produced in all stages of the cement production process, such as during the mining and transportation of raw materials, the processing of raw materials into cement, and the transportation to market for finished products. The terms “cement” and “concrete” are often mixed, but cement is the mineral “glue” that holds concrete together, while concrete is mostly a mixture of varying sized sand, gravel, and stones, also called “aggregates”. Most of the emissions from the cement industry actually come from the production of clinker. Around 95% of Ordinary Portland Cement (OPC), the most common cement type, is clinker. Clinker is produced by heating a mixture of limestone and clay to a high temperature (typically between 1450-1550°C) in a kiln. Emissions arise from both the energy used to heat the kiln, which typically comes from fossil fuels (e.g. coal, natural gas), and the chemical reaction that occurs during the clinkering process (known as the “decarbonation” or “calcination” of limestone), which itself releases carbon dioxide (CO2). In a modern, high tech cement facility, around 60% of the emissions come from the chemical reactions themselves, while the remaining 40% come from the energy supply used to provide the heat to drive the reaction. The clinker production stage of cement manufacturing accounts for between 60-70% of the total CO2 emissions of the industry as a whole. Eliminating the GHGs released from clinker production is therefore the signature challenge facing the cement industry in its future transition to net zero emissions.
Methodology
In broad terms, the major options for reducing the emissions from clinker production include:
- Material efficiency and rational use of cement and cement products
- Material substitution to reduce the amount of high emission clinker in the cement mix
- Fuel switching to use low or zero carbon alternatives for producing the heat for the clinker kiln
- Capturing emissions and storing them to prevent their release to atmosphere
- Non-combustion pathways for cement production
Material Efficiency: Making efficient use of cement and cement products through avoiding the habitual overengineering and waste of material that has become commonplace in contemporary construction is an important pathway to reducing emissions overall from the industry. There are a lack of incentives to rationalize the use of cement as the material is viewed as low cost and the associated emissions from its production are not priced-in to its use. One of the key material efficiency measures from a GHG point of view is better concrete making to minimize pore space between aggregates, which minimizes the amount of cement required to hold them together – this is achieved through multi sized aggregates and better mixing. Material efficiency measures in construction could achieve reductions in cement demand by up to 26% by 2050.
Material Substitution in Portland Cement Clinker (PCC): Ordinary Portland Cement (OPC) is typically 95% clinker. Useful grades of cement can be produced with less clinker (and thus lower emissions overall) by substituting clinker for materials such as fly ash, silica fume, or slag cement. Collectively these substitutes are termed Supplementary Cementitious Materials (SCMs) and produce blended cements that have lower emissions than a “pure” Portland cement. Depending on the application, SCMs can theoretically make up as much as 30-50% of a blended cement by weight, but in practice limited available quantities of SCM materials (which are often waste products from other industrial processes) has meant that to date it is more typical to find concentrations of around 20-30%. Blended cements are in widespread use today. A promising future SCM source is naturally occurring clay. The use of calcinated clay (particularly kaolinite), paired 2:1 with ground limestone, could potentially free up a huge source of SCMs (enabling a push towards 50% substitution of clinker in cement). Calcinated clay cements are at the early commercialization stage of development and available in a limited number of markets.
Material Substitution using Alternative Binders: Various research efforts are underway to completely replace the clinker type used in Portland cement with alternative chemistries that offer similar engineering and technical properties Some of the most promising, in order of technological maturity, include alkali-activated binders, also known as “geopolymers” (early commercialization stage), the carbonation of calcium silicates (technology demonstration stage), and magnesium based cements (early laboratory stage work). In theory, the complete replacement of Portland cement clinker (PCC) would eliminate the release of CO2 to the atmosphere that comes from the calcination reaction stage of cement production, leaving only the emissions from process energy inputs (if any). However, because existing markets and supply chains, as well as construction standards and building codes, are typically based around Portland Cement Clinker (PCC), alternative cement types may face an uphill struggle for rapid adoption.
Fuel Switching to Low or Zero Carbon Alternatives for Kiln Heat: Multiple pathways exist for reducing emissions from clinker production through the substitution of fossil fuels used to achieve high temperatures in the kiln. In order of technological maturity, from the most to the least developed, the options include, waste derived fuels and biomass, which are already widely commercially deployed, heating kilns with solar thermal energy (full prototypes at scale exist), direct electric heating (early prototypes exist), and the partial use of hydrogen (laboratory scale concept). In the European Union the substitution of fossil fuels with waste and forestry residues is already commonplace and makes up around 40% of the energy input to a typical cement kiln. Fuel switching to zero carbon fuels would eliminate the emissions associated with providing process heat energy at the cement plant.
Capturing Emissions: A variety of emissions capture techniques exist to take the flue gasses produced during the cement manufacturing process and prevent their release to the atmosphere. The captured CO2 can then be compressed, transported, and stored in geological formations such as depleted oil and gas fields or deep saline aquifers, or used to manufacture products. The most mature carbon capture technologies for use in the cement industry are chemical adsorption and calcium looping (pre-commercial demonstration) for full CO2 capture of CO2.
Electrochemical Pathways to Cement Production: Two novel approaches exist for the calcination of calcium carbonate at low temperatures. Electrochemical decarbonisation of calcium carbonate uses electrolysis to create lime, with the main byproducts being hydrogen, oxygen and CO2 (in a concentrated waste gas that is easy to capture). This potentially opens the door to a largely electrified pathway for production of a drop-in replacement for Portland cement using decarbonized grid electricity. Another promising approach is the chemical decarbonisation of calcium carbonate. Two groups have currently begun work in this area. The first uses a sodium hydroxide at ambient temperature and pressures, a reaction that produces lime while simultaneously achieving near total (95%) capture of the CO2 in a solid form (sodium carbonate, also known as washing soda). The second group, who have formed a company around their technology, Brimstone Energy, uses chemical decomposition of calcium silicate to produce both lime for cement and magnesium byproducts that are claimed to naturally reattach free CO2 from the air. Electrochemical cement production is currently still at the laboratory test scale
Production and decarbonization
Figure A. Cement production process. Stages with a question mark are not core to the process.
Figure B. Potential methods to reduce the CO2 emissions from cement production.
Source: Paul S. Fennell, Steven J. Davis, Aseel Mohammed, Decarbonizing cement production. Joule, Volume 5, Issue 6, 2021, Pages 1305-1311, ISSN 2542-4351.
https://www.sciencedirect.com/science/article/pii/S2542435121001975
Key Findings
Overview of key findings from the study.
A comprehensive strategy by July 1st 2023
The California Senate Bill 596 requires CARB to develop a comprehensive strategy by July 1st 2023 for the cement sector in California to achieve a greenhouse gas (GHG) emissions intensity 40% below baseline levels by 2035 and net zero GHG emissions by 2045.
Construction of first-of-kind, large-scale near zero GHG clinker
The explicit goal of a zero CO2 emissions cement (ZEC) policy is the transformation of cement manufacturing to near-zero or better CO2 facility emissions (e.g., -90%below current best available technology) by triggering construction of first-of-kind, large-scale near zero GHG clinker production facilities in the near-term (2025-2030) timeframe.
Complementary policies
The ZEC is a complementary policy to existing policies like the WCI cap and trade and tax credits for carbon storage under Section 45Q of the Unites States Internal Revenue Code, with a clear mandate to incentivize investments in critical pre-commercial net zero cement technologies (i.e., at low Technology Readiness Levels, TRLs) that are characterized by steep learning curves and exposure to financial risk.
Extends the logic of the CARB’s Zero Emissions Vehicle (ZEV) program
The ZEC concept explicitly extends the logic of the California Air Resources Board (CARB)’s Zero Emissions Vehicle (ZEV) policy to cement and specifically clinker.
ZEC policy is feasible
On first review a ZEC policy is feasible, and would have high but not complete enforceability
Flexibility over time
Part of the success of the ZEV policy for vehicles to date has been its flexibility over time and the ability to accommodate the issuing of partial credits within the scheme.
Technology-neutral and not overly prescriptive
The language specifying which technologies qualify for credits and how emission reductions are to be achieved should avoid being overly prescriptive and remain as technology-neutral as possible.
The need for champions
Lessons from the ZEV scheme indicate that a company champion, i.e., a likely supplier of partial credits and then builder of the first true near zero emission facility, is required to bring the policy to fruition and carry it through its initial years.
Controlling additional costs
The additional costs of ZECs for clinker producers and retailers of cement and concrete products are meant to be as low as possible while still achieving significant near-zero clinker production by 2035.
Standard sized plant by 2030
By 2030 we estimate the ZEC market needs to be served by at least one standard sized near-zero emissions clinker plant and ideally two for robustness, indicating at least roughly 750 kt and ideally 1.5 Mt per year being produced to meet the goal of market transformation and enable a pathway to net zero by 2050.
Overlapping with California’s Cap and Trade (C&T) system
A ZEC designed solely for California will have significant overlap with California’s Cap and Trade (C&T) system.
Slow, predictable and long-term increase
There is strong evidence from the CARB ZEV scheme that a slow, predictable and long-term increase in stringency that starts low is the most effective and politically durable policy.
In-jurisdiction cement kiln facilities
Given most clinker used in California is made in California, the primary point of enforcement would be at in-jurisdiction cement kiln facilities, which would have to provide purchased ZEC credits or proof of operation of ZEC production, which would entitle them to sell ZEC credits over their direct requirement.
All components legal review
This report is only a first cut preliminary review of the feasibility, and if there is interest a more fulsome design analysis can be prepared, including a legal review of all components depending on the jurisdictional coverage.
Publications
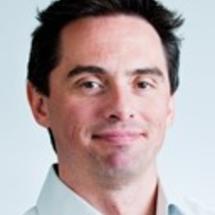
Dr. Chris Bataille
Associate Researcher, IDDRI.org, Paris / Adjunct Professor, Simon Fraser University, Vancouver, Canada
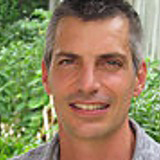
Seton Stiebert
Professional Engineer, Associate International Institute of Sustainable Development (IISD), Ottawa, Canada
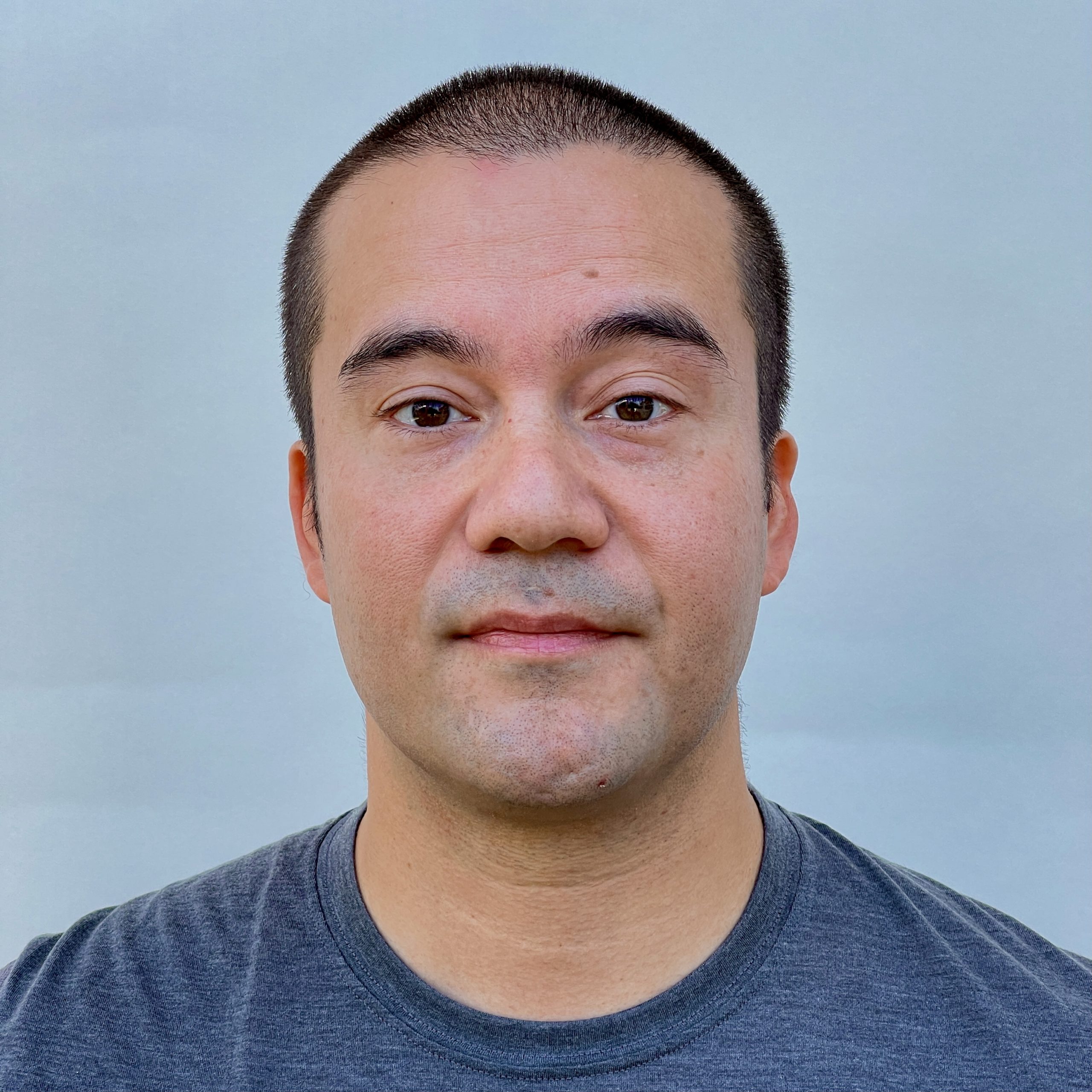
Dr. Francis Li
Principal Engineer, YarCom Inc.
Please contact Dr. Chris Bataille at info@netzeroindustry.org with any question.